Die Casting Process is a manufacturing technique for producing metal components that are used in everyday use.
The Insight Series
We work with our suppliers to develop products across an array of different sectors that rely on varying materials and a range of manufacturing techniques. Undoubtedly, it is always fascinating to see how each of these products is made, whether it is the number of hands that touch the products as it is manufactured or the machines that are utilised as part of the production process.
This month, our insight series is back! We are going to take a look at industrial manufacturing and, in particular, the High Pressure Die Casting Process. Industrial manufacturing is an area that is growing as part of offshore production, with many companies moving to work with Asian suppliers to increase margin at a product level whilst not compromising quality standards.
Inside Industrial Manufacturing
Industrial manufacturing covers a broad range of techniques, processes and machinery. The application is similarly broad – engines, components, panels, wheels, tracks – essentially anything that involves the production of metal parts or plastic parts. Imagine, high temperatures, molten metal and large machines pressing., stamping and casting metal! Given the breadth of the topic, we have decided to focus on just one area for this issue.
High Pressure Die Casting Process
High pressure die casting is a quick, reliable and cost-effective manufacturing process for high volume production of metal components, where molten metal is forced under pressure into a securely locked metal die cavity (tool or mould as some people would have heard). It is then held in place by a powerful press until the metal cools and solidifies. After solidification of the metal, the die is unlocked, opened, and the casting extracted automatically.
Applications
Certainly, high-pressure die casting has wide application encompassing nearly 50% of all light alloy casting production, such as engine components, motorcycle components, household white-goods components, cookware, plumbing & heating, to name only a few. It is applicable to everyday items that can be seen around your house. The workers in the factory work with molten metals and workers wear suitably protective clothing and eyewear.
An example of a high-pressure die casting is provided in the below illustration. Precisely, this shows how the liquid metal is injected with high speed and high pressure into the metal mould. The basic equipment consists of two vertical platens. The bolsters are placed on these platens and this holds the die halves. Out of the two platens, one is fixed and the other movable, this helps the die to open and close.
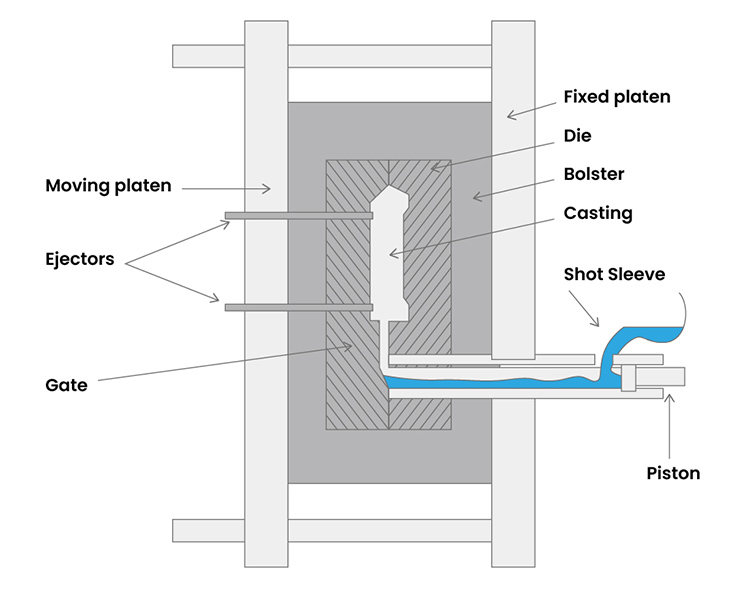
High Pressure Die Casting Process
A specific amount of metal is poured into the shot sleeve and afterward introduced into the die cavity. This is done using a hydraulically driven piston to make the shape required. As you can imagine, unlike a shoe, there is a lot of this manufacturing that is automated, and the workers are there to operate the machinery.
Obviously, different metals require different heat, and these can reach up to 1090C° to cast the metal effectively. The table below shows the temperatures and also the number of products each die will produce before it starts degrading (at that point, you may have issues with the end product). This is important as generally this type of casting process is able to produce large volumes of product before having to replace the die, which itself is expensive.
Jelly Sweets
So, have you ever wondered how jelly sweets are made? HPDC has a broad application and even used to make moulds for sweets. This strawberry jelly mould is made from aluminium (non-ferrous) material which is a versatile material that can be heat treated to give added strength together with lightness, corrosion resistance and high conductivity.
The specific casting temperature of this aluminium is 660.3 degrees C. Raw material is supplied in ingot form (left image) then turned into molten metal in a furnace to be transferred into the shot sleeve for the casting process to commence.
The end product is the mould that food manufacturers use to make a jelly sweet – and lots of them!
Advantages of High-Pressure Die Casting Process
As a manufacturing process, high-pressure die casting has a lot of advantages:
- Low Costs. Given the speed of process, and the level of automation, HDPC is able to produce a lot of products out of one mould compared with other casting processes. This reduces the cost per unit, albeit sometimes the capital investment can be on the higher side.Tolerances
- Tolerances. The process is able to produce close dimensional control (the metal fills the cavity) and good surface finish.
- Weight Flexibility. Given the high pressure used in the production, HDPC is able to produce thin wall finishes, which leads to lighter end product, which still maintains rigidity and functionality.
Summary
Certainly, Industrial manufacturing is a fast-growing sector for offshore manufacturing, particularly across Asia where relative share has grown significantly. This is due to the cost reductions being significant but also overlaid with excellent suppliers and quality standards.
At ET2C, we look to provide our clients with insights across our manufacturing base. We already manufacture a range of industrial products for our clients across multiple markets. For more information, please contact us at contact@et2cint.com.
Cover photo credits: Goodwin Steel Castings . The title and logo have been added to the original image.